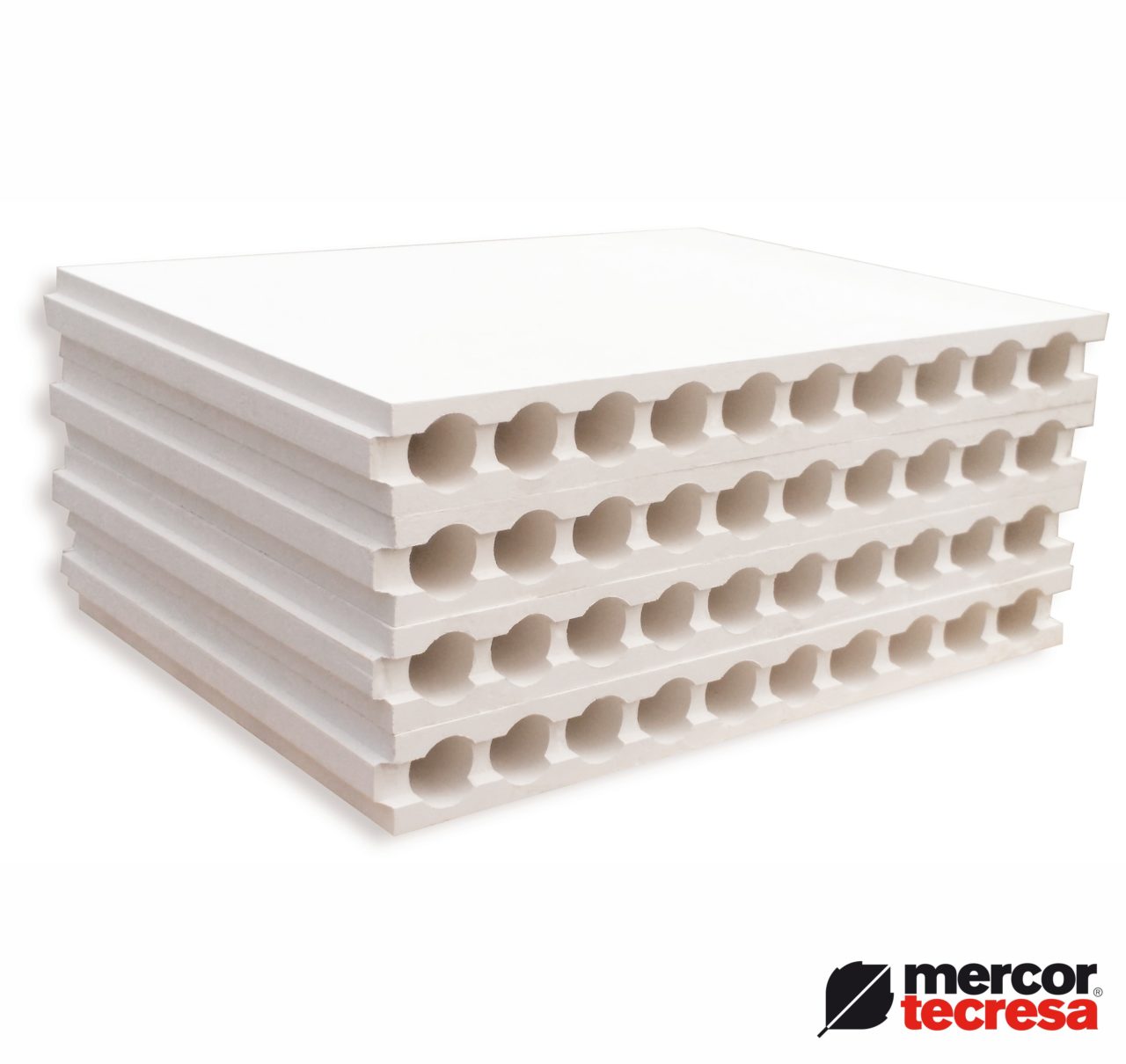
Sectorization of the shafts for services: Alveoltec block®
The shaft for services might have a key role in the propagation of a fire through the different storeys of the building, therefore it is essential to ensure the correct fire sectorization.
There are two approaches to carry out this sectorization:
1.- Perform a horizontal sectorization for each floor. This might be the ideal solution when dealing with shaft of service with electrical installations. However, it is very complex when dealing with mixed installations (electricity, ventilation, PVC downpipes, etc.). The most common system used in this type of installation is High Density Rock Wool + Tecbor® Bonding compound, which we have already mentioned in other Post.
2.- Perform a vertical sectorization to separate the shaft from the building. This sectorization type is an absolute must in the case of multiple installations and you only have to seal the entrances as well as the exits of the installations to the shaft of service using the traditional methods mentioned above.
For this purpose, our R&D department has developed a specific material called ALVEOTEC®. It is a fireproof calcium sulphate block with 660 x 500 mm format and 70 mm thick tongue-and-groove and hollow holes inside that lighten the weight of the system while maintaining its integrity and thermal insulation in contact with fire.
The advantage of this product is its simple installation as it does not require a support structure. It only requires Tecbor® Joint Paste for its fixation to the support construction. Furthermore, its lightness and its small format are ideal to perform a sectorization in not very accessible spaces such as shafts of service.
An important issue, as is the case of ventilation ducts in case of fire, is that inside a shaft of service the pressure differences supported by the walls between the beginning of the shaft and the end of the shaft could be great. Such a distinctive characteristic means that the system must be tested with a specific standard for shaft of service, UNE EN 1366-6, as is the case of our Alveotec system. Very often, shafts are made with Foc type partition systems which, although they comply with Insulation and Integrity, they have not been tested under the shaft of service standard but as partition walls. It is likely that these would not resist the pressures to which the specific test is submitted and, therefore, would not withstand the pressure during a fire.
It is also important to point out that, whenever we close a shaft with a brick masonry wall or similar, it is not possible to plaster the inner face of the shaft since, given its very reduced size, it is very difficult to work inside it. This is problematical, since the CTE establishes resistance to fire on the exposed side and fire might appear on both the inside and the outside of the shaft.
Table F.1. – Fire resistance of walls and brick or silico-calcareous factory partitions | ||||||||
Thickness e of the factory in mm | ||||||||
Type of coating | With air brick | With solid or perforated brick | With clay blocks lightened | |||||
40≤e<80 | 80≤e<110 | e≥110 | 110≤e<200 | e≥200 | 140≤e<240 | e≥240 | ||
Non-coated | (1) | (1) | (1) | REI – 120 | REI – 240 | (1) | (1) | |
Rendering |
By the exposed side | (1) | EI – 60 | EI – 90 | EI – 180 | REI – 240 | EI – 180 | EI – 240 |
On both sides | EI – 30 | EI – 90 | EI – 120 | REI – 180 | REI – 240 | REI – 180 | REI – 240 | |
Trimming |
By the exposed side | EI – 60 | EI – 120 | EI – 180 | EI – 240 | REI – 240 | EI – 240 | EI – 240 |
On both sides | EI – 90 | EI – 180 | EI – 240 | EI – 240 | REI – 240 |
EI- 240
RE – 240
REI – 180
|
REI – 240 | |
(1) Not usual |
With our Alveotec Block there is no need for rendering or posterior trimming, so it perfectly meets the Insulation and Integrity requirements EI-120 by itself, which is customarily required.
Furthermore, the Alveotec® shaft closure system has been tested for both horizontal and vertical shaft of service, which also covers the horizontal sectorization of the wire entry and other facilities in buildings that are sometimes requested by companies supplying electricity, gas, etc.
The system is easy to assemble, cost-effective and of minimal thickness, thus making it the most suitable solution for closing the shaft of service of any building.